Grayscale Digital Light Processing Gradient Printing for Stress Concentration Reduction and Material Toughness Enhancement
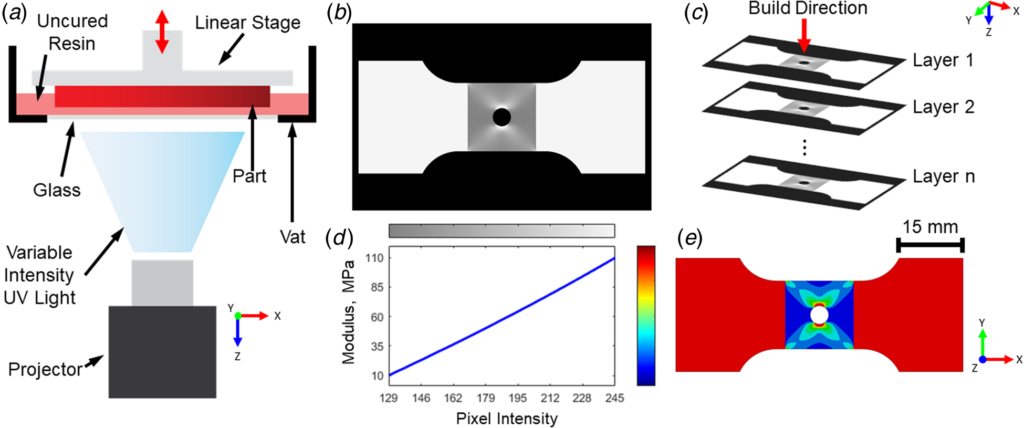
Avoiding stress concentrations is essential to achieve robust parts since failure tends to originate at such concentrations. With recent advances in multimaterial additive manufacturing, it is possible to alter the stress (or strain) distribution by adjusting the material properties in selected locations. Here, we investigate the use of grayscale digital light processing (g-DLP) 3D printing to create modulus gradients around areas of high stress. These gradients prevent failure by redistributing high stresses (or strains) to the neighboring material. The improved material distributions are calculated using finite element analysis. The much-enhanced properties are demonstrated experimentally for thin plates with circular, triangular, and elliptical holes. This work suggests that multimaterial additive manufacturing techniques like g-DLP printing provide a unique opportunity to create tougher engineering materials and parts.
Single-vat single-cure grayscale digital light processing 3D printing of materials with large property difference and high stretchability
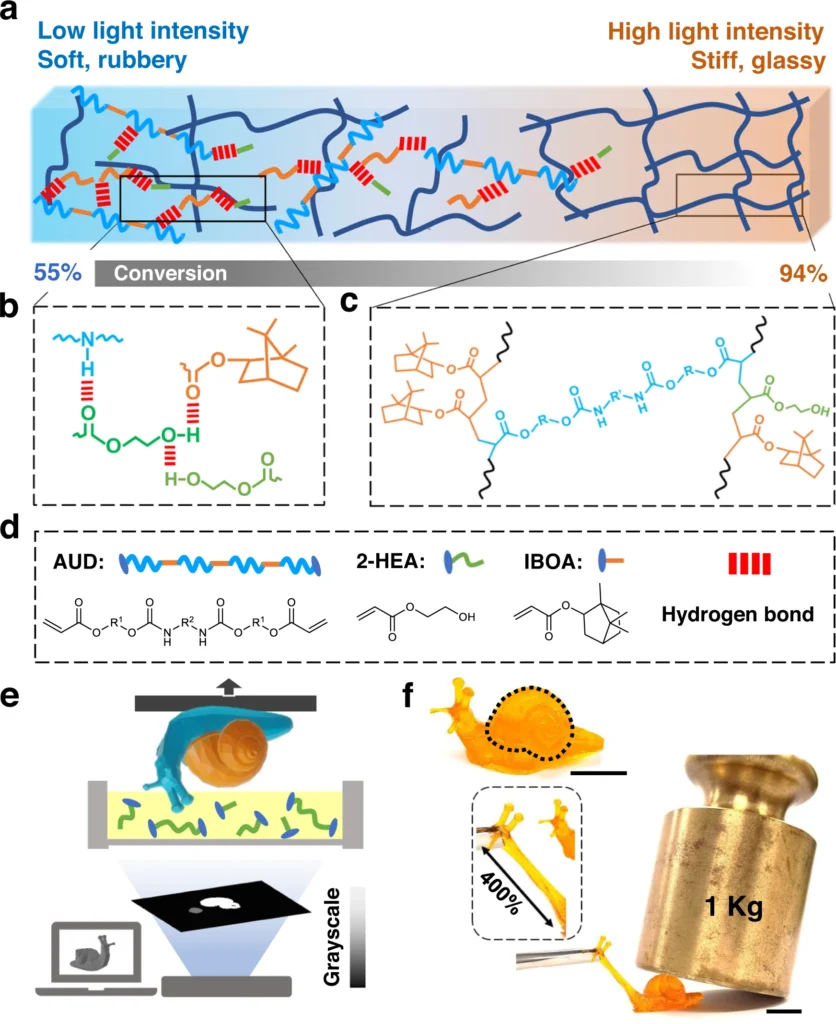
Here, we present a resin design strategy that can be used for single-vat single-cure grayscale digital light processing (g-DLP) 3D printing where light intensity can locally control the conversion of monomers to form from a highly stretchable soft organogel to a stiff thermoset within in a single layer of printing. The high modulus contrast and high stretchability can be realized simultaneously in a monolithic structure at a high printing speed (z-direction height 1 mm/min). We further demonstrate that the capability can enable previously unachievable or hard-to-achieve 3D printed structures for biomimetic designs, inflatable soft robots and actuators, and soft stretchable electronics. This resin design strategy thus provides a material solution in multimaterial additive manufacture for a variety of emerging applications.
Turing pattern–based design and fabrication of inflatable shape-morphing structures
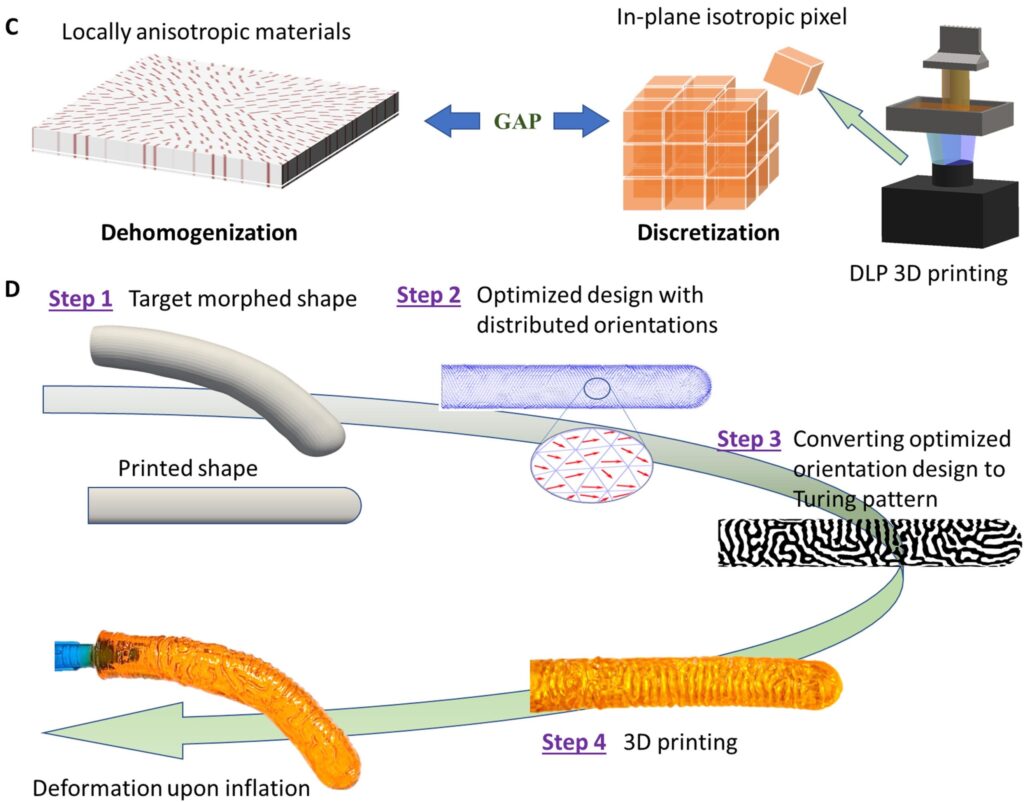
Traditional inflatable structures use isotropic materials with geometrical features to achieve shape morphing. Recently, gradient-based optimization methods have been used to design these structures. These methods assume anisotropic materials whose orientation can vary freely. However, this assumption makes fabrication a considerable challenge by methods such as additive manufacturing, which print isotropic materials. Here, we present a methodology of using Turing patterns to bridge this gap. Specifically, we use Turing patterns to convert a design with distributed anisotropic materials to a distribution with two materials, which can be fabricated by grayscale digital light processing 3D printing. This work suggests that it is possible to apply patterns in biological systems and nature to engineering composites and offers new concepts for future material design.
A hybrid additive manufacturing process for production of functional fiber-reinforced polymer composite structures
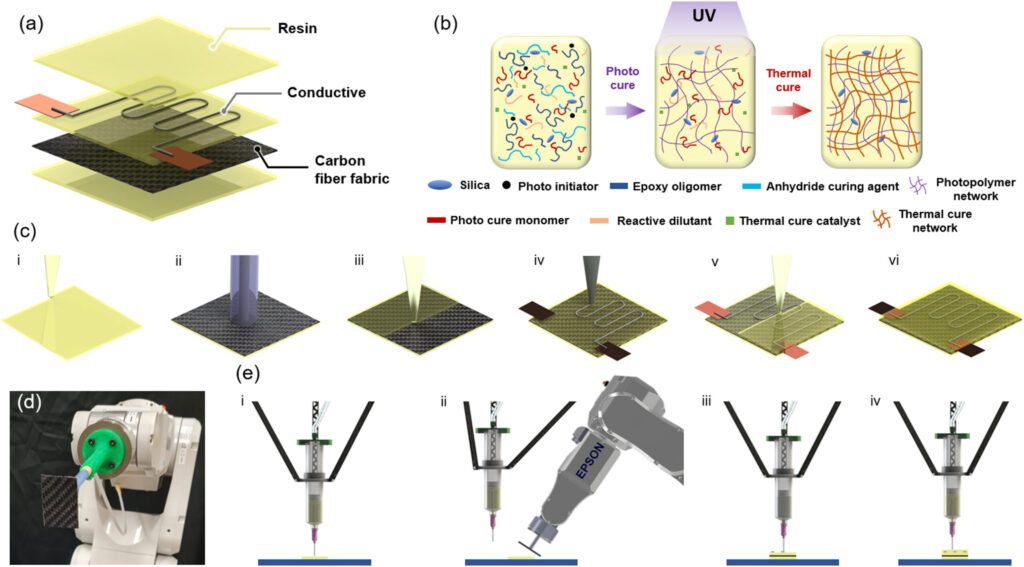
In this paper, we introduce a single-stream hybrid DIW AM technique for the creation of mechanically robust FRPC functional structures where the matrix is DIW 3D printed, and pre-epoxy impregnated (prepreg) woven carbon fiber (CF) fabrics are robotically placed. Additionally, functional components, such as conductive elements, can be readily integrated. We investigated the impact of prepreg woven CF reinforcement on a two-stage photo-thermal thermoset resin matrix on the mechanical characteristics of manufactured FRPCs. We also combined these efforts to fabricate functional structures, including strain sensors for in-situ deformation monitoring, heating elements, and embedded light sensors. This study found that the proposed single-stream hybrid DIW AM process could be a facile approach to fabricate high-strength FRPC functional structures.
Pixel-Level Grayscale Manipulation to Improve Accuracy in Digital Light Processing 3D Printing
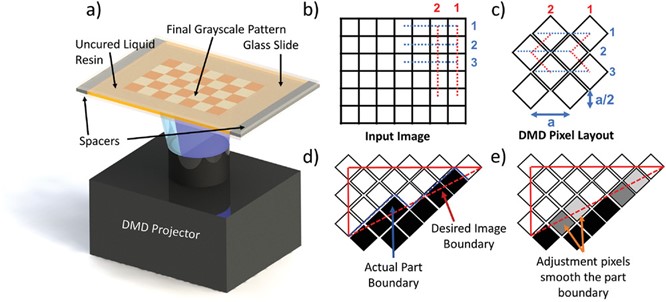
Here, a methodology is developed to enhance accuracy beyond what is typically capable for a given projector resolution by using pixel-level grayscale control to create round features from sharp pixels. A numerical representation of the DLP pixel shape is developed to account for the effects of the incident light patterns. A reaction-diffusion model is then used to predict the printed shapes before and after grayscale enhancement. This model is used to determine the optimal pixel intensities to match a target shape. Finally, the minimum feature size allowed by the proposed method is explored. The promising results represent an important step forward in raising DLP printing to higher accuracy, which will allow the fabrication of functional and structural components with smaller features or smoother faces.
Unstructured Direct Ink Write 3D Printing of Functional Structures with Ambient Temperature Curing Dual-Network Thermoset Ink
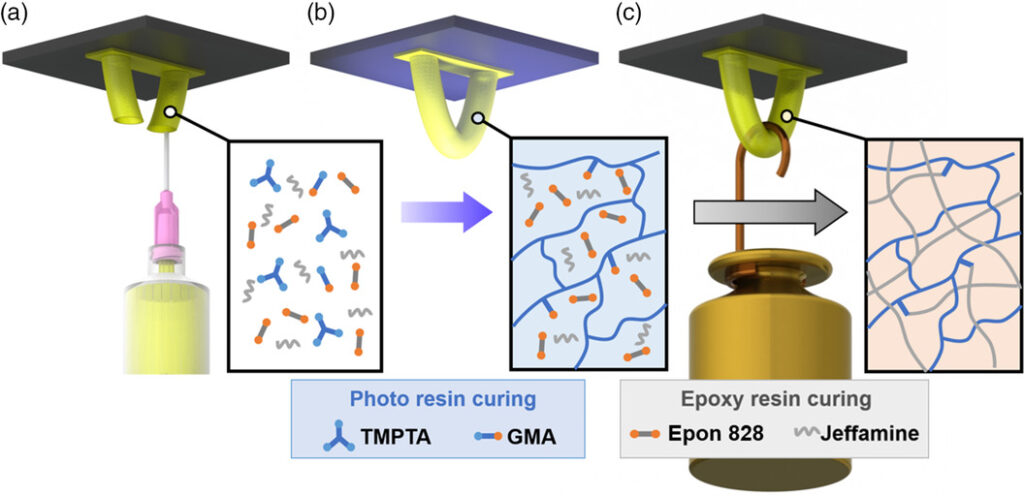
A versatile, reconfigurable direct ink writing (DIW) manufacturing method is developed in tandem with a two-stage hybrid ink designed to fabricate high-strength, self-supporting parts in unconventional printing spaces such as underneath a build surface or horizontally. This two-stage hybrid DIW ink combines a photopolymer and a tough epoxy resin. The photopolymer can cure rapidly to enable layer-by-layer printing of complex structures. It also possesses adequate adhesion to allow the fabrication of large volume structures on a diversity of substrates including acrylic, wood, glass, aluminum, and concrete. The epoxy component can cure after 72 h in ambient conditions with further increased adhesion strengths. The capabilities of the reconfigurable DIW extrusion nozzle method to print complex structures in inverted and horizontal environments are demonstrated. Finally, via addition of DIW-deposited conductive paths, a functional 3D-printed structure capable of in situ deformation monitoring is created. This work has the potential to be used for applications such as appending new parts to existing structures for increasing functionality, repair, and structure health monitoring.
Enabling direct ink write edible 3D printing of food purees with cellulose nanocrystals
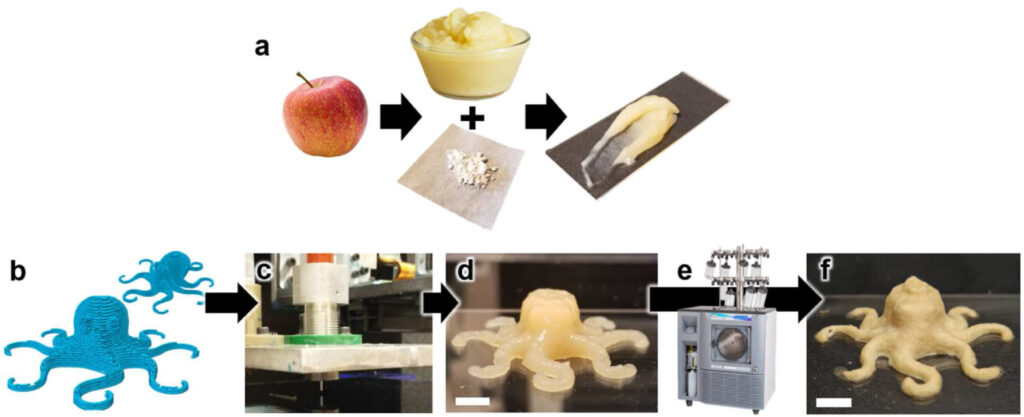
In this paper, we present cellulose nanocrystals (CNCs) as a safe and renewable rheological modifier capable of enabling DIW 3D printing of a variety of foodstuffs, specifically spinach puree, tomato puree, and applesauce, and using freeze-dry to obtain final solid structures. We first analyzed the rheological characterization of foodstuffs combined with varying volume fractions of CNCs to produce shear-thinning, printable inks. The print quality of different inks was then analyzed via image processing techniques. Finally, we demonstrated the capability of CNC-laden inks by printing a variety of structures, including multi-material structures with integrated packaging. This study found that CNCs are an effective rheological additive which promoted shear-thinning, viscous behavior in the studied edible feedstocks necessary for DIW 3D printing of self-supporting edible structures.
4D Printing of Freestanding Liquid Crystal Elastomers via Hybrid Additive Manufacturing. Advanced Materials
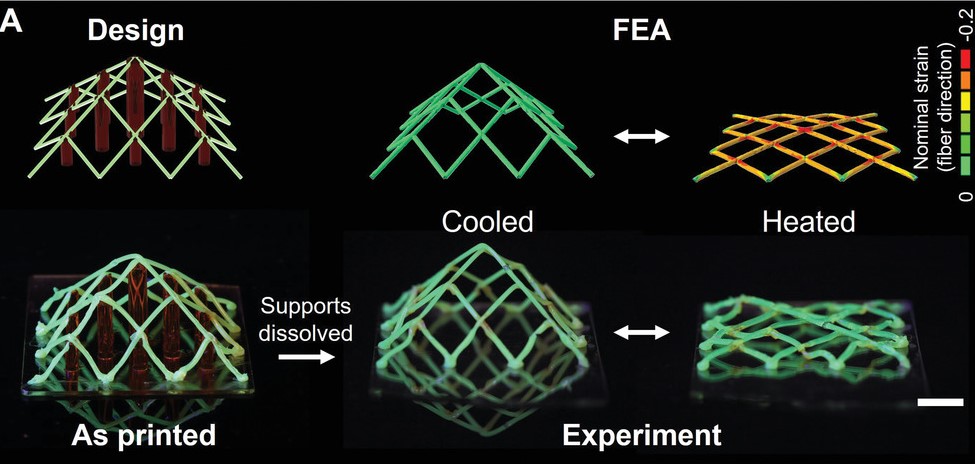
Liquid crystal elastomers (LCE) are appealing candidates among active materials for 4D printing, due to their reversible, programmable and rapid actuation capabilities. Recent progress has been made on direct ink writing (DIW) or Digital Light Processing (DLP) to print LCEs with certain actuation. However, it remains a challenge to achieve complicated structures, such as spatial lattices with large actuation, due to the limitation of printing LCEs on the build platform or the previous layer. Herein, a novel method to 4D print freestanding LCEs on-the-fly by using laser-assisted DIW with an actuation strain up to −40% is proposed. The combination of DIW-printed functionally freestanding LCEs with the DLP-printed supporting structures thus provides new design freedom and fabrication capability for applications including soft robotics, smart structures, active metamaterials, and smart wearable devices.
A Hybrid Additive Manufacturing Process for Production of Functional Fiber-Reinforced Polymer Composite Structures
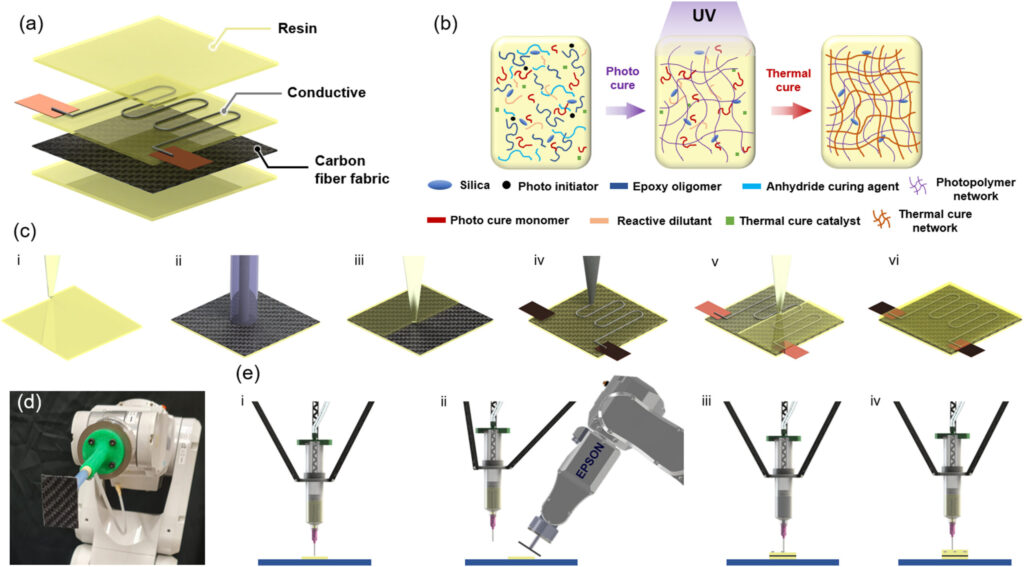
In this paper, we introduce a single-stream hybrid DIW AM technique for the creation of mechanically robust FRPC functional structures where the matrix is DIW 3D printed, and pre-epoxy impregnated (prepreg) woven carbon fiber (CF) fabrics are robotically placed. Additionally, functional components, such as conductive elements, can be readily integrated. We investigated the impact of prepreg woven CF reinforcement on a two-stage photo-thermal thermoset resin matrix on the mechanical characteristics of manufactured FRPCs. We also combined these efforts to fabricate functional structures, including strain sensors for in-situ deformation monitoring, heating elements, and embedded light sensors.
4D Printed Multifunctional Composites with Cooling-Rate Mediated Tunable Shape Morphing
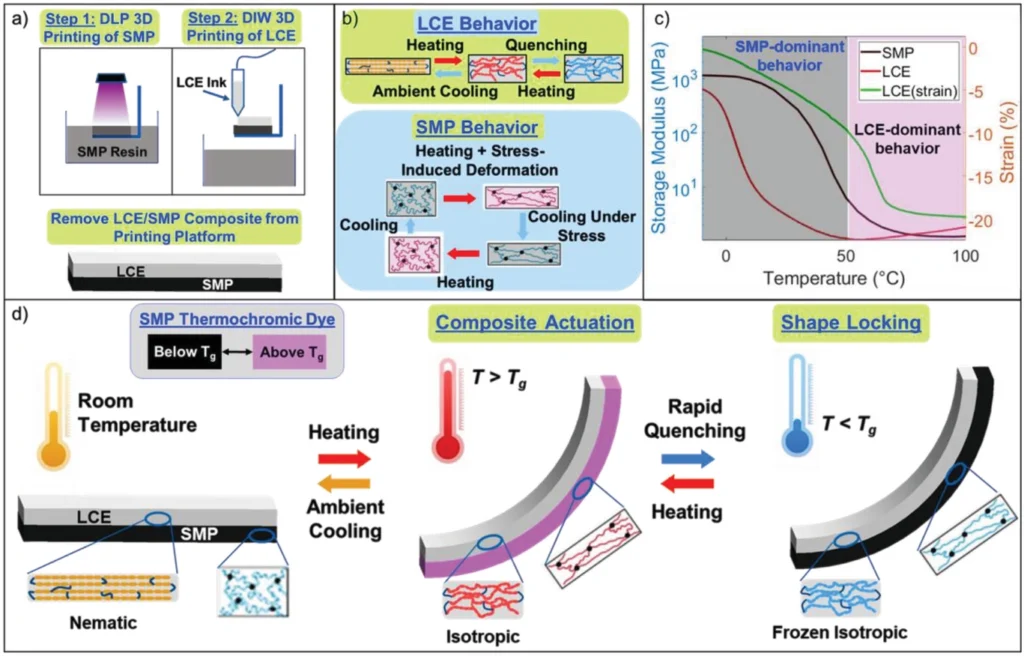
Smart materials including liquid crystal elastomers (LCE) and shape memory polymers (SMP) have long been used as the primary components of multifunctional composites because of their shape and property changes in response to external stimuli. However, LCEs can generate rapid and reversible shape changes but are soft and require a constant temperature to retain their deformed shape; SMPs have favorable mechanical properties but few can achieve reversible actuations. Moreover, both LCEs and SMPs have limited capability for tunable shape morphing. In this work, 4D printing is leveraged to create an LCE-SMP composite that can achieve not only rapid and reversible shape changes, but also cooling-rate regulated tunable shape morphing. The latter is achieved by harnessing the distinct time-dependent thermomechanical properties of LCEs and SMPs.
Enabling direct ink write edible 3D printing of food purees with cellulose nanocrystals
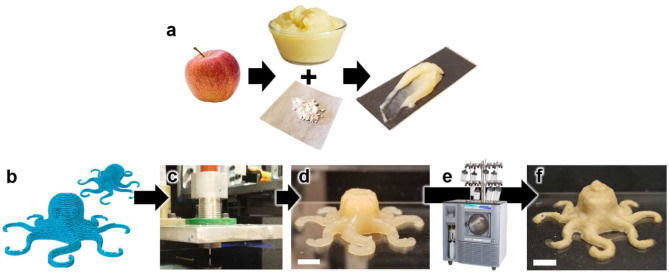
In this paper, we present cellulose nanocrystals (CNCs) as a safe and renewable rheological modifier capable of enabling DIW 3D printing of a variety of foodstuffs, specifically spinach puree, tomato puree, and applesauce, and using freeze-dry to obtain final solid structures. We first analyzed the rheological characterization of foodstuffs combined with varying volume fractions of CNCs to produce shear-thinning, printable inks. The print quality of different inks was then analyzed via image processing techniques. Finally, we demonstrated the capability of CNC-laden inks by printing a variety of structures, including multi-material structures with integrated packaging. This study found that CNCs are an effective rheological additive which promoted shear-thinning, viscous behavior in the studied edible feedstocks necessary for DIW 3D printing of self-supporting edible structures.
A reaction–diffusion model for grayscale digital light processing 3D printing
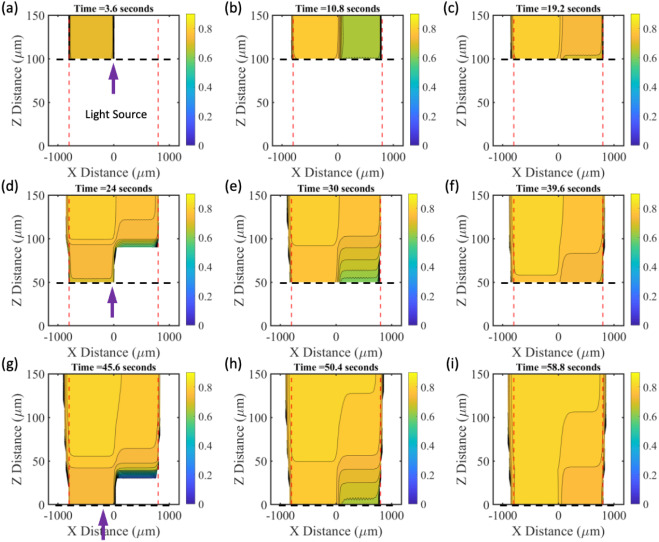
In this paper, a photopolymerization reaction–diffusion model is developed and used in conjunction with experiments to investigate the coupled effects of light propagation, chemical reaction rates, and species diffusion during g-DLP 3D printing. The agreement between experimental and model predictions of simple quantities of interest shows that the model can capture the overcure due to free-radical and other species diffusion during printing when grayscale patterns are employed. This model lays the groundwork for future extensions that can incorporate more complex coupled physics such as heat transfer, volume shrinkage, and material property evolution, which are critically important in utilizing g-DLP 3D printing for the fabrication of high-performance parts which excellent geometric and material property tolerances.
Montgomery, S.M., Hamel, C.M., Skovran, J. and Qi, H.J., 2022. A reaction–diffusion model for grayscale digital light processing 3D printing. Extreme Mechanics Letters, 53, p.101714.
Machine Learning-Evolutionary Algorithm Enabled Design for 4D-Printed Active Composite Structures
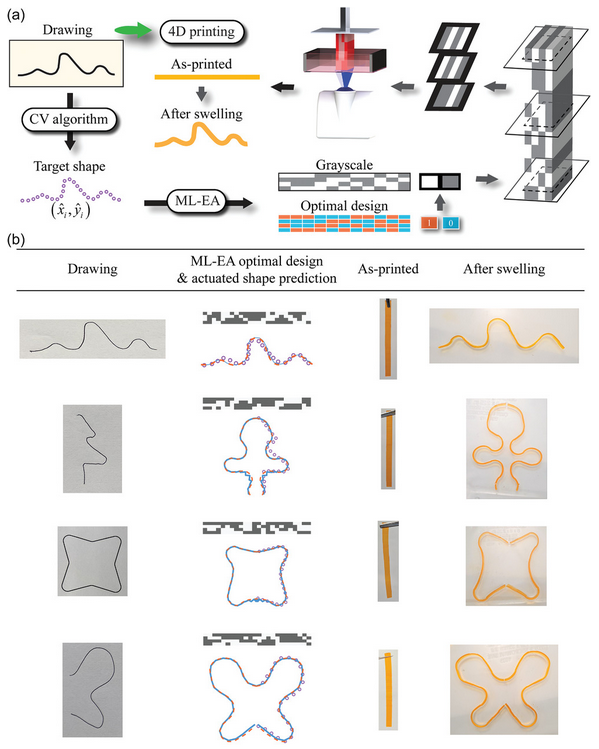
Here, a novel machine learning (ML) and evolutionary algorithm (EA) based approach is presented to guide the design process of active composites. A recurrent neural network (RNN) based ML model whose training dataset is acquired by finite element simulations is developed for the forward shape-change prediction. EA empowered with ML is then used to solve the inverse problem of finding the optimal design. For multiple target shapes with different complexities, the ML-EA approach demonstrates high efficiency. Combining the ML-EA with computer vision algorithms, a new paradigm is presented that streamlines design and 4D printing process where active straight beams can be designed based on hand-drawn lines and be 4D printed that transform into the drawn profiles under the stimulus. The approach thus provides a highly efficient tool for the design of 4D-printed active composites.
Multi-Color 3D Printing via Single-Vat Grayscale Digital Light Processing
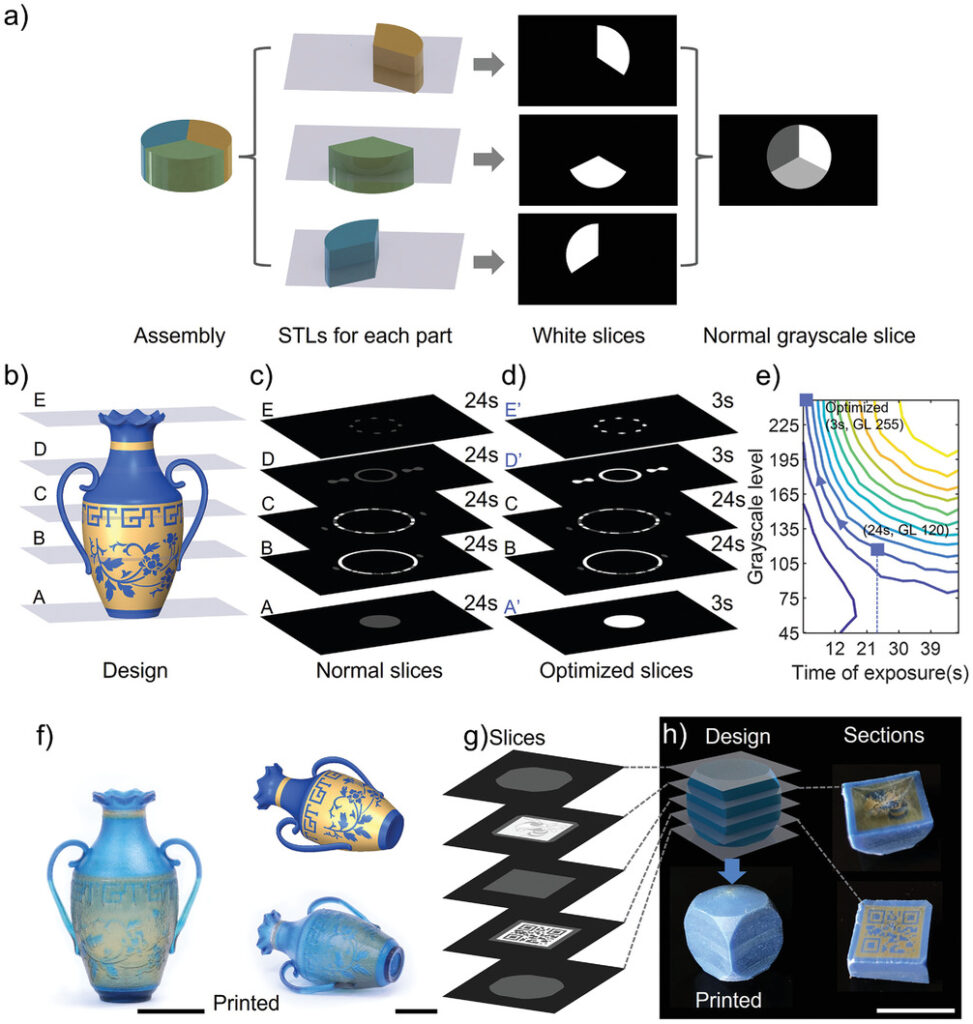
In this study, a single-vat multi-color DLP 3D printing by using an anthraquinone-based dye is realized. The dye can be oxidized by the free radicals released from photoinitiators under ultraviolet light and change the color from blue to yellow. This color-changing mechanism permits a graded spectrum of colors as concomitants of the photopolymerization process during DLP printing by controlling the light dose without using extra vats or devices. Multi-color demonstrations, such as engineering stress simulation results in 3D and multi-color vases, are successfully fabricated, showing great versatility and efficiency.
Integrating digital light processing with direct ink writing for hybrid 3D printing of functional structures and devices
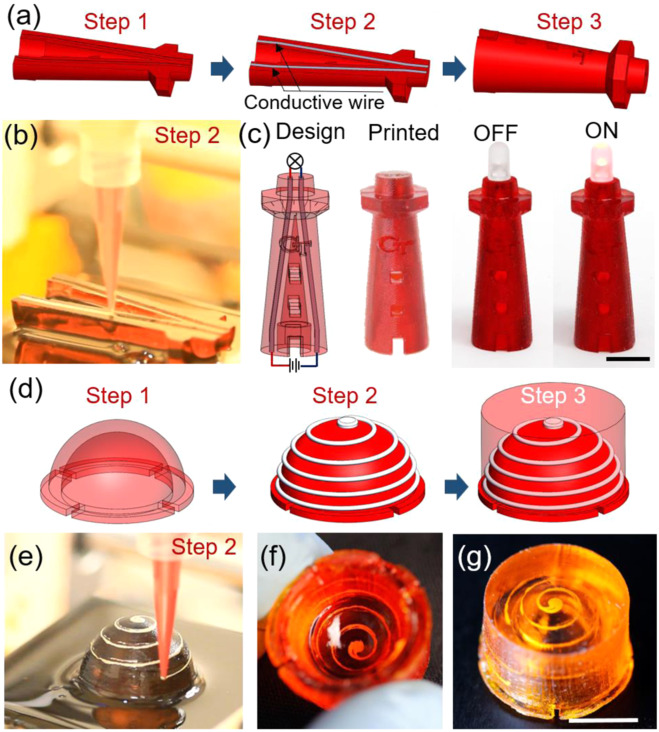
n this paper, we present a new hybrid multi-material 3D printing system that consists of a top-down digital light processing (DLP) printing and a direct ink writing (DIW) printing to fabricate composite structures and unique devices in a single printing job. The vat photopolymerization-based DLP printing allows for high-speed and high-resolution printing of a material matrix with complex geometry. The material extrusion-based DIW printing enables the printing of functional material, including liquid crystal elastomers (LCEs) and conductive silver inks. With this hybrid 3D printing system, a wide choice of inks and resins can be used to print functional composites with tunable mechanical properties, enhanced interfacial bonding, and multifunctionality. We demonstrate that composites prototype, active soft robots, circuit-embedding architectures, and strain sensors can be successfully printed. This work provides a new and robust approach for 3D printing of multi-functional devices for broad applications in soft robotics, electronics, active metamaterials, and biomedical devices.
The m4 3D Printer: A multi-material multi-method additive manufacturing platform for future 3D printed structures
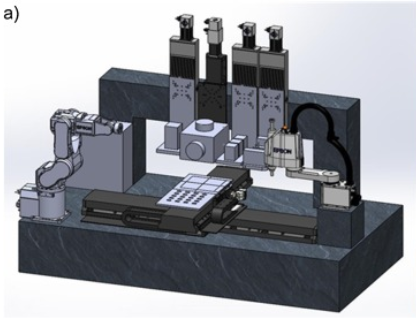
Many existing 3D printing technologies only allow one material to be printed at one time, while many applications require the integration of different materials, which sometimes cannot be printed by one AM technology. In this paper, a novel multi-material multi-method (m4) 3D printer comprised of multiple AM technologies is presented as a solution to the current limitations. This printer fosters the advancement of AM by combining materials traditionally unable to be printed concurrently while adding functionality to printed parts.
Design for 4D printing: Modeling and computation of smart materials distributions
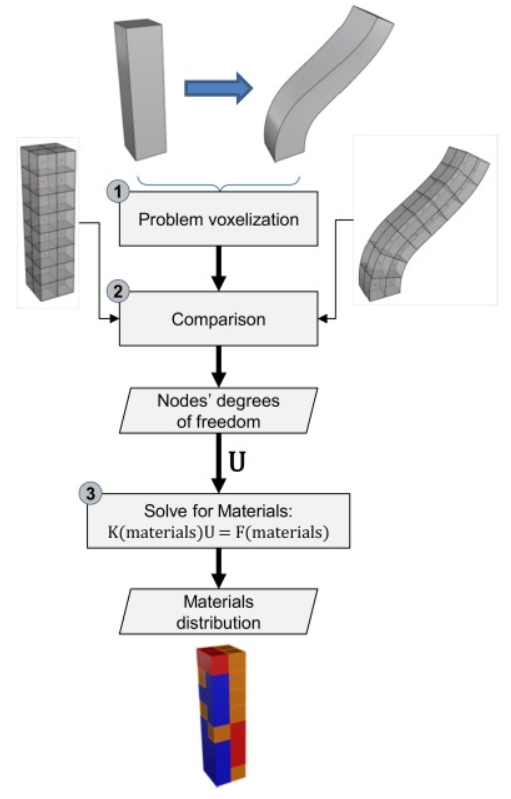
The material complexity allowed by additive manufacturing (AM) has made smart materials (SMs) processing easier, giving birth to the so called 4D printing (4DP). But, for this expanded design space to be embraced by designers, there is the need to make SMs modeling and simulation easier, especially in conceptual design. Here, a twofold contribution is made to design for 4DP. First a computational tool, VoxSmart, employing the previously developed theoretical framework is introduced. Given a source shape and a target shape, a set of materials, and a stimulus, finding the right material distribution that yields the appropriate transformation under stimulus is quite challenging. Addressing this issue is the focus of this work’s second contribution.
Sossou, G., Demoly, F., Belkebir, H., Qi, H. J., Gomes, S., & Montavon, G. (2019). Design for 4D printing: Modeling and computation of smart materials distributions. Materials & Design, 108074.
Dynamic Photomask-Assisted Direct Ink Writing Multimaterial for Multilevel Triboelectric Nanogenerator
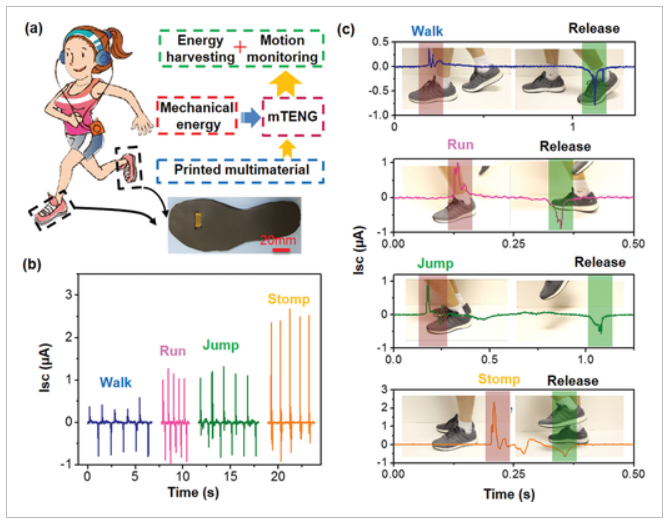
Triboelectric nanogenerator (TENG) devices are extensively studied as a mechanical energy harvester and self‐powered sensor for wearable electronics and physiological monitoring. Here, the printed multimaterial matrix for multilevel mechanical‐responsive TENG with on‐demand reconfiguration of shape is reported. Multimaterial structures with location‐specific properties, such as tensile modulus, failure stress, and glass transition temperature for controlled deformation, crack propagation path, and sequential shape memory, are directly printed. This work provides a new approach to combine multimaterial 3D printing with TENG devices for functional wearable electronics as energy harvester and sensors.
Chen, K., Zhang, L., Kuang, X., Li, V., Lei, M., Kang, G., … & Qi, H. J. (2019). Dynamic Photomask‐Assisted Direct Ink Writing Multimaterial for Multilevel Triboelectric Nanogenerator. Advanced Functional Materials, 1903568.
3D printing of auxetic metamaterials with digitally reprogrammable shape
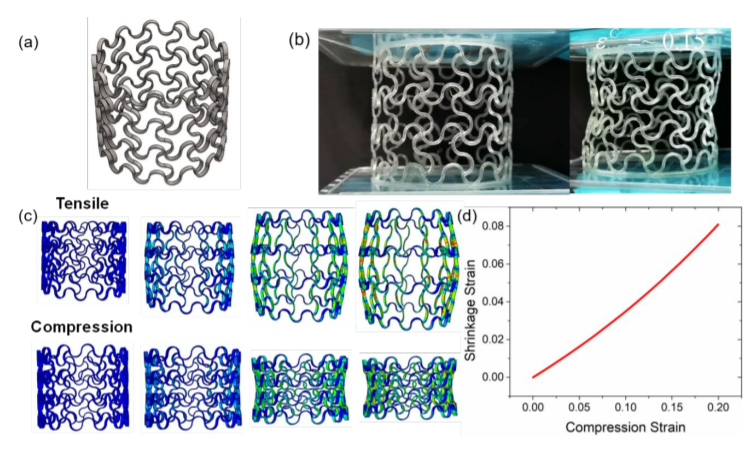
Two-dimensional lattice structures with specific geometric features have been reported to have a negative Poisson’s ratio, termed as auxetic metamaterials, i.e., stretching induces expansion in the transversal direction. In this paper, we designed a novel auxetic metamaterial, which by utilizing the shape memory effect of the constituent materials, the in-plane moduli and Poisson’s ratios can be continuously tailored. Finally, we designed and fabricated gradient/digital patterns and cylindrical shells and used the auxetics and shape memory effects to reshape the printed structures.
Lei, M., Hong, W., Zhao, Z., Hamel, C. M., Chen, M., Lu, H., & Qi, H. J. (2019). 3D printing of auxetic metamaterials with digitally reprogrammable shape. ACS applied materials & interfaces.
Long Liquid Crystal Elastomer Fibers with Large Reversible Actuation Strains for Smart Textiles and Artificial Muscles
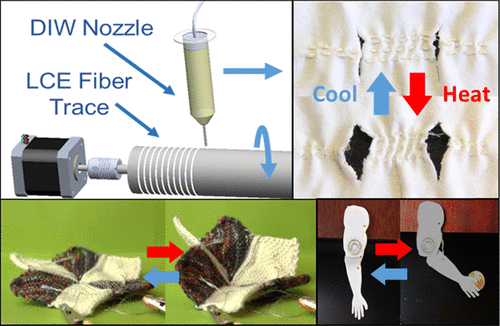
A method for fabricating long, soft, and reversibly actuatable liquid crystal elastomer (LCE) fibers by using direct ink write (DIW) printing was developed. Upon optimizing the ink viscosity and DIW printing parameters, long fibers (up to 1.5 m long from the laboratory) were obtained. The LCE fibers were knit, sewn, and woven to form a variety of smart textiles. The fiber was also used to mimic bicep muscles with both large activation force and activation strain. By incorporating further intelligent characteristics, such as conductivity and biosensing into a single fiber, the LCE fibers could be potentially used for smart clothing, soft robotics, and biomedical devices.
Roach, D. J., Yuan, C., Kuang, X., Li, V. C. F., Blake, P., Romero, M. L., … & Qi, H. J. (2019). Long Liquid Crystal Elastomer Fibers with Large Reversible Actuation Strains for Smart Textiles and Artificial Muscles. ACS applied materials & interfaces.
Reaction-Diffusion Model for Thermosetting Polymer Dissolution through Exchange Reactions Assisted by Small-Molecule Solvents
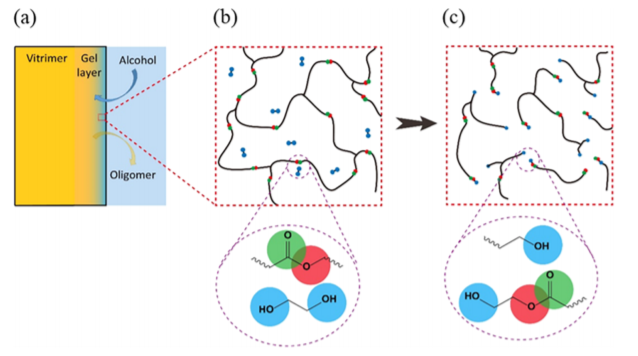
Thermosetting polymers involving dynamic bonds or exchange reactions (also known as vitrimers) can be fully dissolved in a solvent utilizing a small-molecule-participated bond-exchange reaction (BER). However, dissolution is a complex process that couples chemical reactions with the diffusion featured by varied diffusivity both in time and dimension. Here, a reaction-diffusion model is developed for the vitrimer dissolution in alcohol via transesterification. This work provides a deep insight into the reaction-diffusion process, which can be used to guide the future development and optimize recycling processes using dynamic bonds.
Hamel, C. M., Kuang, X., Chen, K., & Qi, H. J. (2019). Reaction-Diffusion Model for Thermosetting Polymer Dissolution through Exchange Reactions Assisted by Small-Molecule Solvents. Macromolecules.
Three-Dimensionally Printed Mechanical Metamaterials With Thermally Tunable Auxetic Behavior
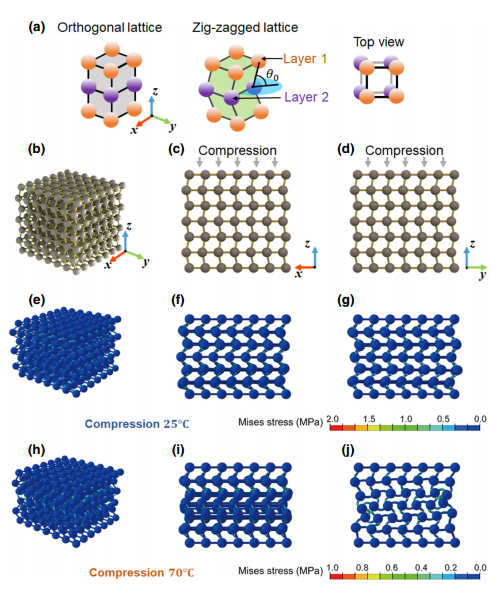
In this work, we demonstrate the dynamic and on-demand regulation of mechanical metamaterials through a combination of structural design and multimaterial 3D printing. We design a soft periodic lattice metamaterial containing two distinct deformation modes. One deformation mode is controlled by the zig-zagged topological defects, and the other one is controlled by the thermal activation of the responsive materials imbedded in the lattice. We believe our design principle opens up a new route for the exploration of metamaterials exhibiting extraordinary and programmable mechanical behaviors.
Zhao, Z., Yuan, C., Lei, M., Yang, L., Zhang, Q., Chen, H., Qi, H. J., & Fang, D. (2019). Three-Dimensionally Printed Mechanical Metamaterials With Thermally Tunable Auxetic Behavior. Physical Review Applied, 11(4), 044074.
Design for 4D printing: A voxel-based modeling and simulation of smart materials
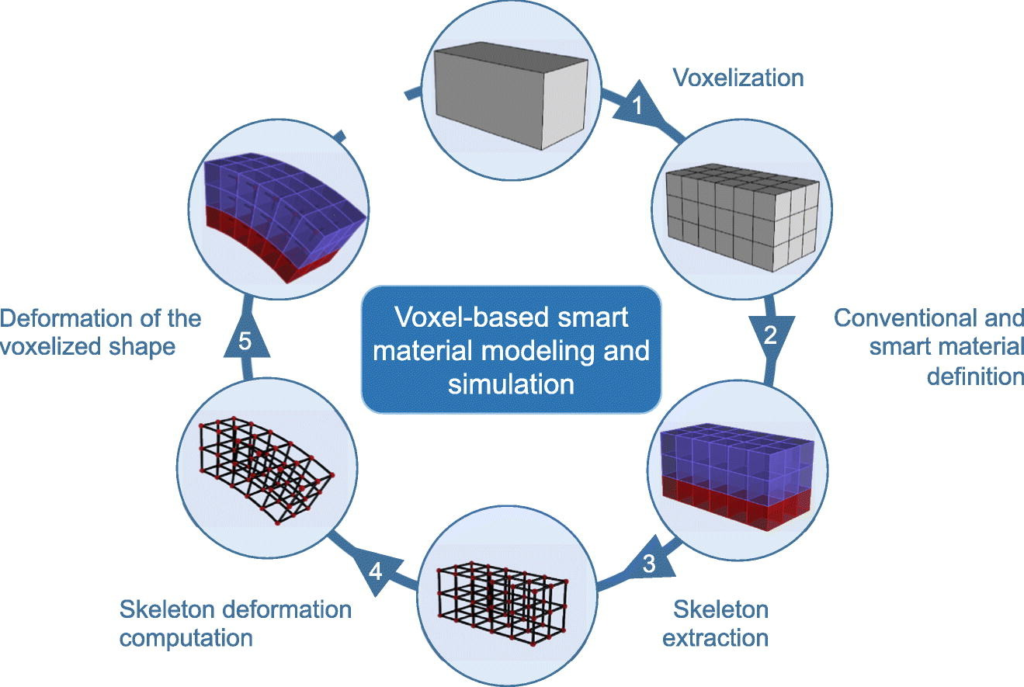
In this article, a modeling framework for simulating smart materials (SMs) and conventional materials behaviors on a voxel basis is proposed; this allows for arranging materials in any distribution and rapidly evaluating the behavior of the distribution. Homogeneous and heterogeneous objects made of conventional materials and SMs were modeled and simulated. These simulations have a speed reasonable for the design iterations needed in conceptual design phase and they yield results in good agreement with physics.
Sossou , G., Demoly, F., Belkebir, H., Qi, H. J., Gomes, S., & Montavon, G. (2019). Design for 4D printing: A voxel-based modeling and simulation of smart materials. Materials & Design, 107798.
Cellulose Nanocrystals Support Material for 3D Printing Complexly Shaped Structures via Multi-Materials-Multi-Methods Printing
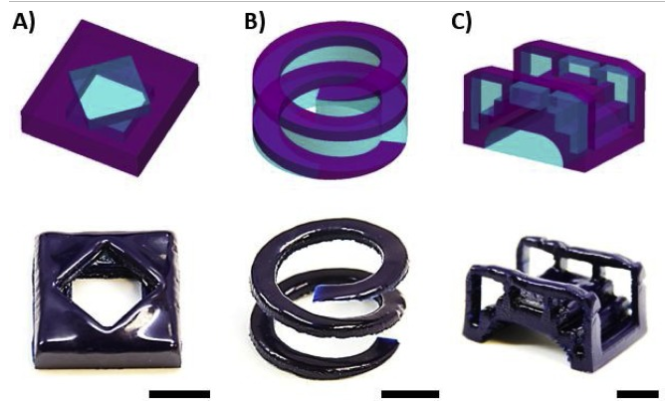
To fabricate highly complex structures, sacrificial support material is usually needed. However, traditional petroleum-based support materials are unsustainable, non-recyclable, and difficult to be completely removed from the target structure after 3D printing. In this work, we demonstrate how cellulose nanocrystal (CNC) gels can address all three of these challenges. We show that the CNC gel can easily be removed with water even in highly confined environments.
Li, V. C. F., Kuang, X., Hamel, C. M., Roach, D., Deng, Y., & Qi, H. J. (2019). Cellulose Nanocrystals Support Material for 3D Printing Complexly Shaped Structures via Multi-Materials-Multi-Methods Printing. Additive Manufacturing.
Machine-learning Based Design of Active Composite Structures for 4D Printing
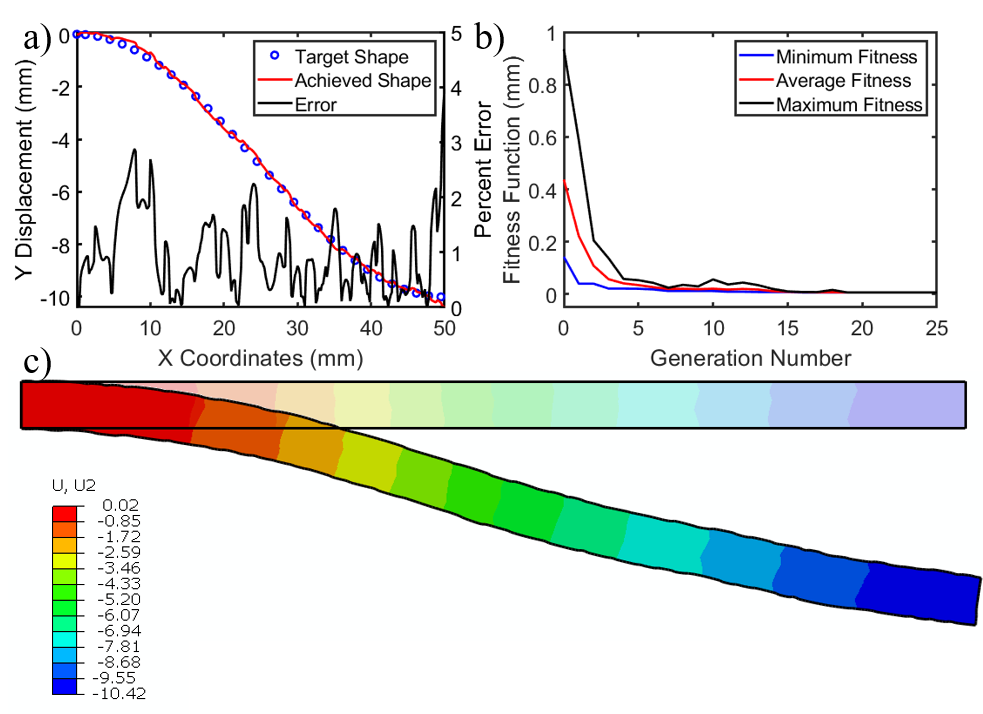
In this work our aim is to find ideal material distributions for attaining a target shape during 4D printing. Due to the non-linear response of the material and the inverse nature of the problem traditional optimization approaches are limited to one type of material or environmental stimulation. These restrictions and recent advances in computer power inspired our group to use machine learning based techniques to find optimal material distributions for 4D printing applications. Briefly, we utilize evolutionary algorithms in conjunction with finite element simulations to discover ideal material distributions.
Hamel, C., Roach, D., Long, K., Demoly, F., Dunn, M., & Qi, J. (2019). Machine-learning Based Design of Active Composite Structures for 4D Printing. Smart Materials and Structures.
A Viscoelastic Model for Hydrothermally Activated Malleable Covalent Network Polymer and its Application in Shape Memory Analysis
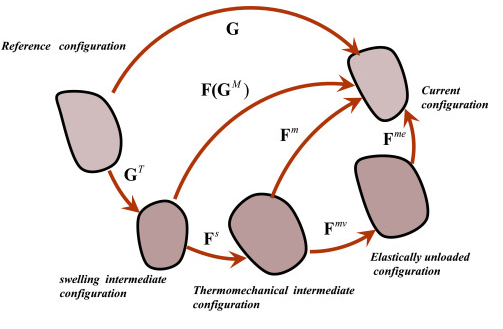
Recently proposed polyimine-based malleable covalent network polymers (MCNPs) show water or temperature induced shape reforming under low temperatures. This work provides understandings and design guidelines for the hydrothermal-activated malleable covalent network polymer.
Mao, Y., Chen, F., Hou, S., Qi, H. J., & Yu, K. (2019). A Viscoelastic Model for Hydrothermally Activated Malleable Covalent Network Polymer and its Application in Shape Memory Analysis. Journal of the Mechanics and Physics of Solids.
Extraction of Biolubricant via Chemical Recycling of Thermosetting Polymers

Extracting biolubricant of dicarboxylic acid ester via chemical recycling of thermoset waste can reduce environmental pollution and alleviate petrochemical consumption.
Kuang, X., Guo, E., Chen, K., & Qi, H. J. (2019). Extraction of Biolubricant via Chemical Recycling of Thermosetting Polymers. ACS Sustainable Chemistry & Engineering , 7 (7), 6880-6888
3D printed cellulose nanocrystal composites through digital light processing
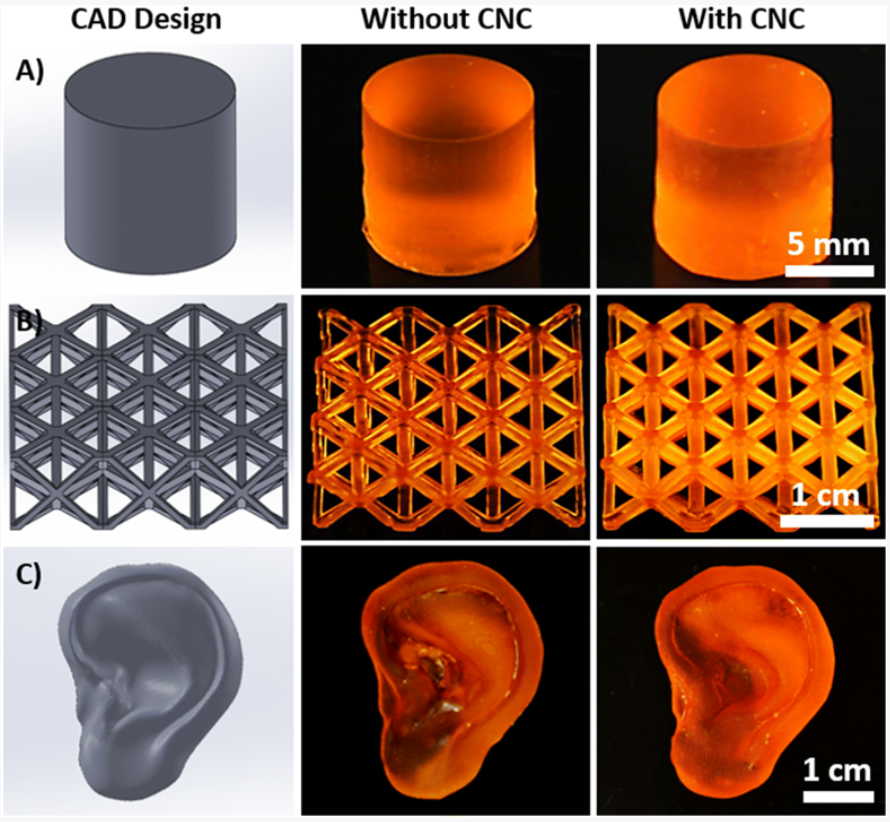
Cellulose Nanocrystals (CNC) have received significant attention due to their high Young’s modulus, high strength, biocompatibility, and renewability. These properties make them ideal as a reinforcement phase for polymer composites. This work utilized the digital light processing (DLP) 3D printing approach to fabricate CNC reinforced PEGDA glycerol composites. Mechanical testing results indicated that mechanical properties of DLP 3D printed composites were improved by CNC incorporation.
Enabling direct ink write edible 3D printing of food purees with cellulose nanocrystals
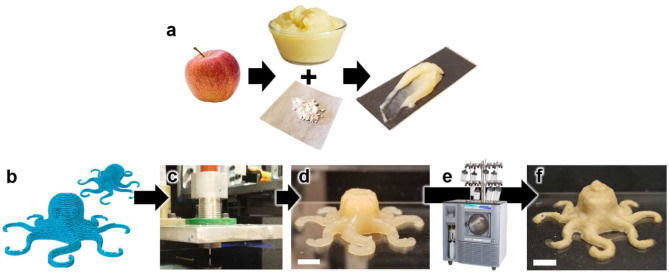
In this paper, we present cellulose nanocrystals (CNCs) as a safe and renewable rheological modifier capable of enabling DIW 3D printing of a variety of foodstuffs, specifically spinach puree, tomato puree, and applesauce, and using freeze-dry to obtain final solid structures. We first analyzed the rheological characterization of foodstuffs combined with varying volume fractions of CNCs to produce shear-thinning, printable inks. The print quality of different inks was then analyzed via image processing techniques. Finally, we demonstrated the capability of CNC-laden inks by printing a variety of structures, including multi-material structures with integrated packaging. This study found that CNCs are an effective rheological additive which promoted shear-thinning, viscous behavior in the studied edible feedstocks necessary for DIW 3D printing of self-supporting edible structures.